Did you know India pumped out over $110 billion worth of electronics in the last year? That’s a seven-fold jump compared to just a decade ago. Walk into any phone store—chances are, at least one big brand was assembled, if not made, in India. People like to talk about smartphones, but TVs, wearables, and even some laptops are rolling off factory lines from Tamil Nadu to Uttar Pradesh.
It’s not hype. Major global brands—think Apple and Samsung—are shifting big parts of their supply chain to Indian soil. Why does this matter? With supply chain headaches from China and global demand not slowing down, India’s stepping into a huge opportunity. But is the growth solid, or are there hidden cracks? If you’re in business—or just curious where that next phone or TV actually comes from—knowing what’s behind India’s electronics surge could help you stay ahead.
- Why India’s Electronics Sector is Booming
- Government Push and Policy Moves
- What’s Being Made—and Where
- Real Challenges Behind the Numbers
Why India’s Electronics Sector is Booming
India’s electronics industry isn’t growing by accident. It’s a mix of high local demand, smart policies, and a global shift in manufacturing. Smartphone sales in India crossed 175 million units last year. Homegrown brands and international giants are fighting for a piece of that massive market, which keeps factories busy.
But consumer demand is just one part. India’s electronics manufacturing is getting a real push because companies want alternatives to China. Costs in China are rising and trade tensions make it risky. India’s labor advantage (wages still lower than China) and a young workforce make it attractive to global brands.
The numbers say it all:
Year | Electronics Manufacturing Output (USD) |
---|---|
2015 | ~$30 billion |
2024 | ~$110 billion |
That’s more than three times growth in less than a decade. The industry growth isn’t just about phones, either—there’s a boom in smart TVs, audio gear, and computer parts. Plus, India is starting to make a mark with export numbers. In 2023, electronics exports crossed $28 billion, with mobile phones making up nearly half that total.
Another reason for this surge: supply chain localization. More and more, companies set up local suppliers for things like batteries, displays, and chip assembly. This shrinks the import bill and keeps jobs in the country. If you’re a supplier or a startup, it’s a time to look at gaps that need filling in the India electronics supply chain.
So, why now? Simply put: huge local demand, global supply chain shifts, skilled workers, and government programs (we’ll cover those next). If you’re eyeing business in India or just want to understand the hype, these are the main reasons the sector is buzzing.
Government Push and Policy Moves
The surge in India electronics manufacturing isn’t an accident—it’s very much by design. The Indian government has been on a mission to put the country on the global manufacturing map, and boy, they’ve pulled out all the stops. The PLI (Production Linked Incentive) scheme, first rolled out in 2020 for electronics, is a simple but powerful idea: make more goods in India, get cash rewards from the government. Over 30 global and Indian brands jumped in, with Apple suppliers like Foxconn, Wistron, and Pegatron opening or expanding factories here—mainly in Tamil Nadu and Karnataka.
The goal? Lower the country’s reliance on imports and boost exports. The government aims to make India a $300 billion electronics manufacturing hub by 2026. It’s not just talk—exports have already doubled over the last three years, with smartphones leading the pack. India actually overtook Vietnam as the world’s second largest mobile manufacturing country, right behind China.
Besides the PLI, the government created policies like the Scheme for Promotion of Manufacturing of Electronic Components and Semiconductors (SPECS), which literally helps with funding new factories for chips, displays, and parts that usually came from abroad. And for anyone setting up a new plant, the Modified Electronics Manufacturing Clusters (EMC 2.0) scheme gives you cheaper land, shared power and logistics, and better infrastructure—game changers for any new or expanding factory.
Policy | Launch Year | Main Benefit |
---|---|---|
PLI for Electronics | 2020 | Cash incentives for manufacturers |
SPECS | 2020 | Financial support for components & semiconductors |
EMC 2.0 | 2020 | Cheaper land & better infrastructure |
If you’re thinking of joining the electronics game, these policies cut your costs, speed up approvals, and connect you with skilled workers across established hubs. There’s a long way to go before India matches China’s scale, but if you look at these numbers and policy rollouts, the momentum is clearly on India’s side.
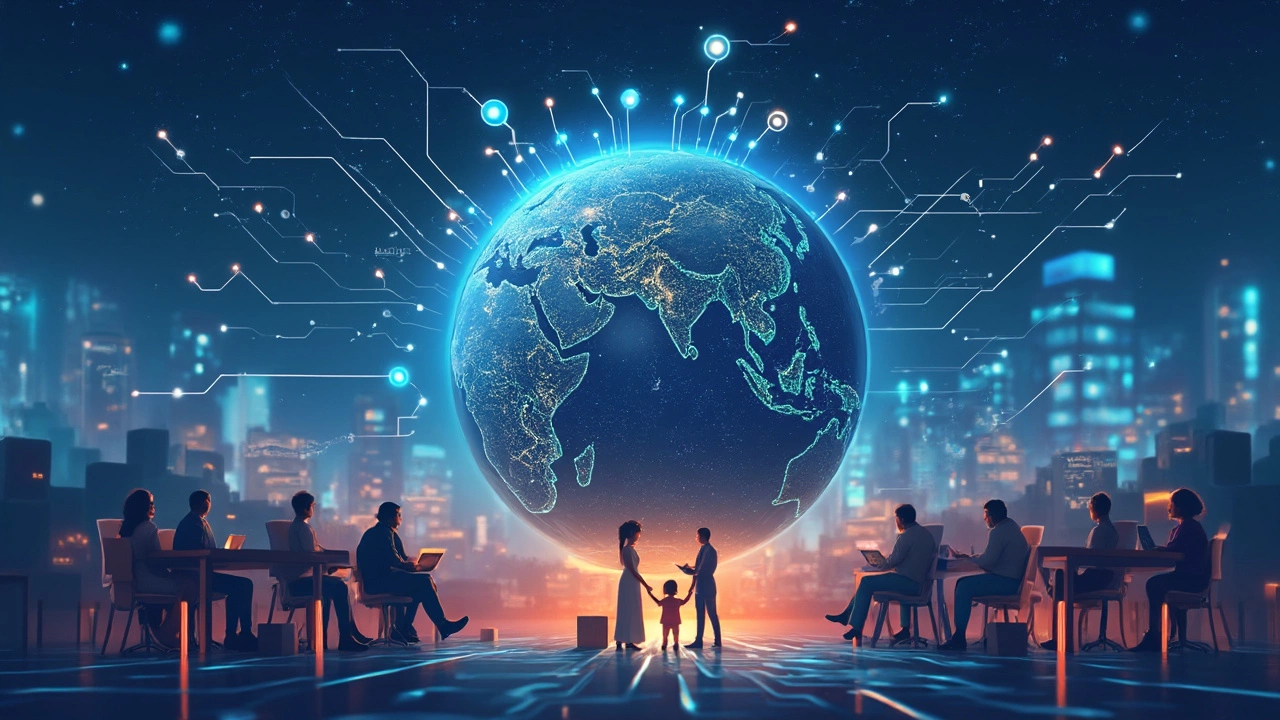
What’s Being Made—and Where
India isn’t just assembling smartphones anymore—though that part is booming. The country’s electronics manufacturing scene now covers smartphones, TVs, wearables, tablets, LED lighting, routers, and even some semiconductor packaging. The jaw-dropping bit? Over 99% of smartphones sold in India in 2024 were actually made in the country, not imported.
Here’s what’s popping off the lines in key regions:
- Noida & Greater Noida (UP): Think massive smartphone plants run by Samsung, Oppo, Xiaomi, Lava, and Dixon. There’s also a surge in contract manufacturers here building devices for big global brands.
- Sriperumbudur & Chennai (Tamil Nadu): Apple’s iPhones are assembled here largely thanks to Foxconn and Pegatron. TVs and home appliances roll out of these factories too.
- Bangalore (Karnataka): Major hub for wearables, smart home gadgets, and some chip design units. Multinational tech companies love this region for its talent pool.
- Pune & Maharashtra belt: Home to many LED lighting and consumer electronics producers, plus a few companies handling specialty semiconductors related to the auto sector.
Local players aren’t getting left behind. Dixon, Bharat FIH, and Optiemus are now some of the biggest electronics manufacturing partners for both Indian and international brands. This means more devices aren’t just assembled, but designed and supported right here.
Check out this quick breakdown of what’s being made and where as of March 2025:
Region | Main Products | Key Companies |
---|---|---|
Noida & Greater Noida | Smartphones, TVs | Samsung, Dixon, Oppo, Lava |
Chennai & Sriperumbudur | iPhones, TVs, ACs | Foxconn, Samsung, Pegatron |
Bangalore | Wearables, routers, IoT devices | Bosch, Wistron, Qualcomm |
Pune & Maharashtra | LEDs, auto electronics | Flex, Tata Electronics, Varroc |
If you’re eyeing the India electronics ecosystem, notice how manufacturing is spreading out, not stuck in just one region. This makes supply chains more reliable and creates local jobs where they didn’t exist before. For businesses looking to tap into this, teaming up with contract manufacturers in these hotspots is usually the fastest way to get off the ground.
Real Challenges Behind the Numbers
The headlines about India electronics keep getting bigger, but not every stat tells the whole story. There's no shortage of energy in the factories, yet the backbone—core parts and components—still comes from outside the country. About 65% of India's electronic components are imported, most from China and Southeast Asia. If supply chains get bumpy, so does local manufacturing.
There’s also the talent crunch. While there’s no lack of engineers, companies often complain that fresh graduates need a lot of extra training before they can handle advanced work, especially in semiconductors. India’s handful of good electronics design companies can’t keep up with the demand from manufacturers looking to build more complex products locally.
Infrastructure is another big speed bump. Even a quick drive near some factory hubs in Noida or Chennai will show you patchy roads and unreliable power. The government’s putting up fancy new plants, but the lack of basic support systems slows down production and jacks up costs.
- Manufacturing still relies heavily on imported printed circuit boards (PCBs), semiconductors, and displays.
- Customs often delay parts at ports, sometimes for weeks, due to overzealous inspections and red tape.
- The scale is growing fast, but local suppliers can’t always keep up, which forces big companies to import in bulk.
It’s not all gloom, but let’s talk numbers. India wants to hit $300 billion in electronics manufacturing by 2026, but as of April 2025, just a quarter of this target comes from value added on Indian soil. Most of the rest is assembly, with imported bits getting attached together for export.
Challenge | Current Status |
---|---|
Component Import Dependency | 65% imported |
Skilled Workforce | Shortage for advanced roles |
Customs Delays | Up to several weeks at ports |
Value Addition | Only 25% local |
For anyone thinking about investing in industry growth or export, the tip is simple: dig deeper than the top numbers. Look at where your components and people will come from, and factor in how you’ll handle those well-known bottlenecks. If you plan for the rough patches, you’re way ahead of the pack.
Write a comment