Delving into the world of manufacturing can be as intricate as it is fascinating. In 2025, the landscape of manufacturing is shaped by three foundational components that propel it forward: the people who work within it, the processes that drive production, and the ever-evolving technology that underpins operations. These components not only define the efficiency and output of a manufacturing system but also determine its adaptability in an environment that is continuously transforming.
The relationship between these elements is dynamic, orchestrating a dance that taxes both creativity and discipline. While workers lend their ingenuity and commitment, processes are tailored meticulously to reduce waste and increase output. Meanwhile, technology serves as the backbone that supports and sometimes even revolutionizes these time-honored practices. Join us as we explore the symbiotic relationship between these elements, shedding light on how government schemes play a pivotal role in nurturing this synergy and ensuring industry standards soar to even greater heights.
- The Role of Human Resources
- Optimizing Manufacturing Processes
- Technology Integration in Production
- Government Schemes Supporting Manufacturing
- Future Trends in Manufacturing Systems
The Role of Human Resources
In the vast expanse of the manufacturing system, human resources serve as the beating heart, energizing every facet of the production ecosystem. The modern factory environment has evolved dramatically from the days when manual labor was its sole driving force. Today, skilled workers are not only operating machinery but are also integral in the planning, innovation, and optimization processes. Their roles have expanded to include problem-solving, resource management, and enhancing workplace efficiency. The emphasis on human resources within these systems isn't just about assigning tasks. It's about harnessing the potential each individual possesses and aligning it with the company's objectives.
What sets human resources apart in this dynamic environment is their adaptability to change. Employees regularly undergo training programs and workshops, many of which are subsidized by government schemes designed to keep the workforce competitive and efficient. As technology integrates deeper into manufacturing, employees are trained to work alongside sophisticated systems, often evolving their roles from operators to overseers and analysts. This transition underscores the importance of continuous learning, a hallmark of thriving industries worldwide. In fact, recent surveys show a significant increase in productivity and job satisfaction among manufacturing personnel involved in regular upskilling programs.
The governmental influence in shaping the manufacturing workforce cannot be understated. Various initiatives aim to foster a culture of innovation and collaboration within the facility walls. These schemes often promote interdepartmental exchanges, encouraging a cross-pollination of ideas which can lead to breakthrough innovations. With the increasing focus on sustainability, employees are urged to participate in eco-friendly practices within their roles, a testament to their evolving significance beyond traditional responsibilities. For instance, in 2024, a well-structured program led to a 15% reduction in energy consumption in participating factories.
"Our people are our greatest asset, and investing in their growth is paramount to achieving organizational excellence," said John Richards, a seasoned manufacturing executive, highlighting the crucial yet often understated role human resources play in production success.
Ensuring worker health and safety remains a pivotal concern as modern machinery becomes more complex and potentially hazardous. Human resources departments are tasked with ensuring a culture of safety, and it comes as no surprise that facilities with robust safety protocols tend to report fewer incidents, thus maintaining productivity. Moreover, companies are increasingly recognizing the importance of mental well-being, instituting support systems and programs to foster a healthy work-life balance. Such measures not only improve quality of life for the workforce but also augment productivity and retention rates, reflecting a direct impact on the bottom line.
In conclusion, the role human resources play in the manufacturing sector is multifaceted and ever-evolving. As workplaces become more tech-driven, the need for a skilled and adaptable workforce is more critical than ever. With the support of government schemes and initiatives focusing on workforce development, the potential for human resources to influence and propel the manufacturing industry toward greater heights is immense and promising. The integration of their expertise, creativity, and commitment is what truly powers the machinery of the modern manufacturing world.
Optimizing Manufacturing Processes
Manufacturing processes form the crux of any production line, serving as the backbone that allows all other components to function in harmony. In 2025, a keen focus lies in optimizing these processes to reach peak productivity while minimizing waste. It's akin to fine-tuning a musical orchestra—everything must work in sync to produce a harmonious symphony. The modern manufacturing system integrates lean principles to streamline processes, ensuring that every step from raw material procurement to final product assembly is efficient and devoid of unnecessary complexity.
Implementing these optimal processes involves a detailed examination of the supply chain. This includes understanding the lifecycle of materials, from how they are sourced, transported, and ultimately transformed. Today's savvy manufacturers place a high premium on transparency, which not only enhances efficiency but also allows for greater accountability. Techniques such as Just-In-Time (JIT) inventory help to minimize storage costs and reduce wastage, ensuring materials arrive only as needed. Similar methodologies like Six Sigma provide statistical approaches to eliminate defects and enhance quality control, fostering precision at every stage.
Technology plays an indispensable role in enhancing these processes. Automation, for example, represents a significant leap forward, allowing repetitive tasks to be completed with unerring accuracy and speed. Robots equipped with artificial intelligence take on roles that demand precision, freeing human resources to engage in more strategic, decision-making roles that elevate the entire manufacturing system. Smart sensor technology monitors equipment health, predicting maintenance needs before they escalate into costly breakdowns. The integration of such technology is crucial, making the system not only efficient but also predictive in its operations.
Another dimension of process optimization lies in fostering a culture of continuous improvement. Manufacturing depends not only on the processes themselves but also on the mindset that surrounds them. Companies that invest in training programs encourage a workforce that is proactive in identifying inefficiencies. Continuous feedback loops ensure that processes remain flexible and adaptable, keeping pace with changing demands and technological advancements. Embracing such a culture ensures sustainable growth and a robust competitive advantage in the market.
Government Support and Schemes
In various regions, government schemes provide the infrastructure and support necessary to foster optimal manufacturing processes. These initiatives often provide financial incentives, encouraging companies to invest in modern equipment and upskilling their workforce. For instance, the German "Industrie 4.0" initiative exemplifies how such schemes can bolster industrial growth by promoting digitization and automation in manufacturing. A quote from a prominent industry expert highlights this:"Government interventions, when crafted well, can be the catalyst for industry revolutions—spurring investment, innovation, and in many cases, leveling the playing field for small players," mentioned by James Hanson, a well-known industry analyst.
Data further emphasizes the impact of government schemes in optimizing manufacturing operations. In a 2024 survey conducted by Global Manufacturing Institute, 76% of manufacturers reported enhanced efficiency after upgrading processes in alignment with governmental schemes. The same study showcased a 22% return on investment within the first year of adoption, thanks to increased productivity and reduced operational costs. Such statistical insights underscore the tangible benefits of optimizing manufacturing processes, fueled by both innovation and supportive legislation.
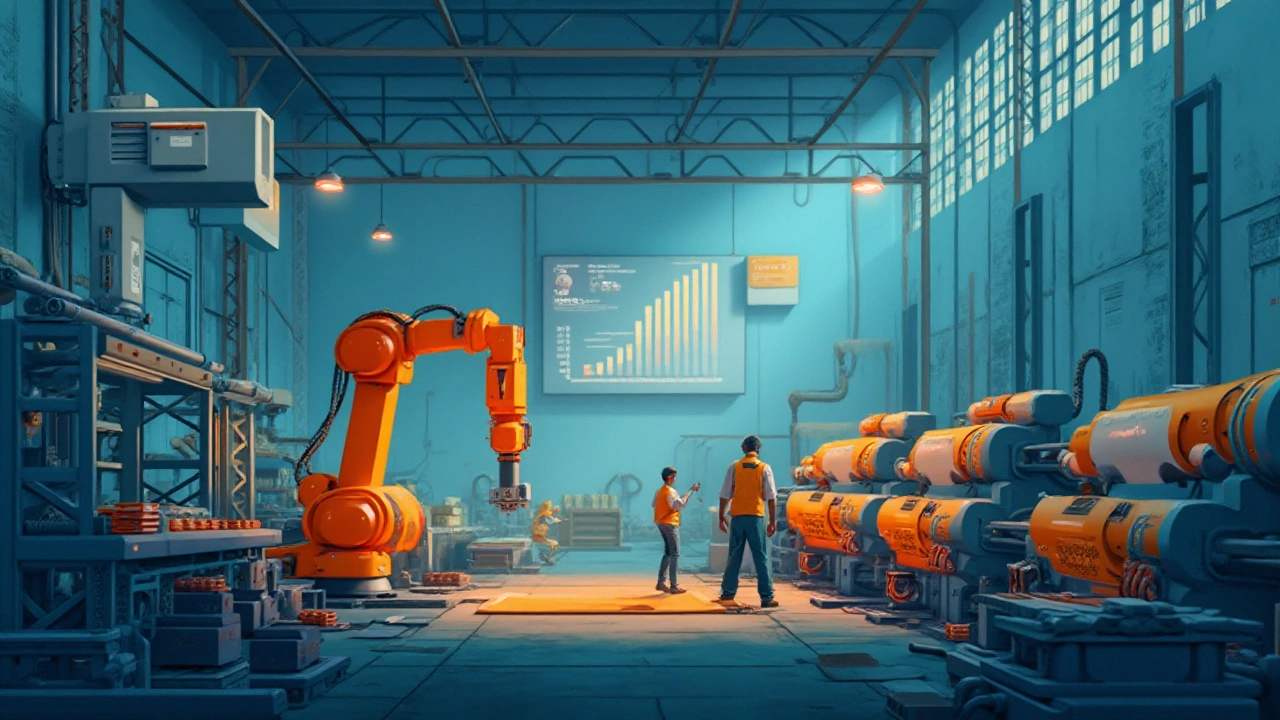
Technology Integration in Production
In the exciting world of modern manufacturing, the infusion of technology has reshaped how industries operate, laying the groundwork for unprecedented levels of efficiency and innovation. The contemporary production environment is not a static space; it thrives on the integration of advanced tools, robotics, and information technology. A significant focus lies on automation, where robotics and AI play a crucial role in quality control, assembly lines, and material handling. These machines are continuously evolving, enabling quicker and more precise production cycles that were once unimaginable. The integration doesn't stop at machinery and automation. Systems such as IoT (Internet of Things) tie machinery with data analytics, giving manufacturers insights into performance metrics, predicting maintenance needs, and enhancing energy efficiency. Such capabilities greatly reduce downtime and operational costs, proving to be an indispensable part of a successful manufacturing system.
Going beyond the physical aspects, there is a seamless marriage between software and hardware that paves the way for remarkable flexibility in the production process. Cloud computing facilities and software platforms allow for real-time data sharing and collaboration among teams, regardless of their geographical location. This ease of access to information fosters innovation, allowing teams to refine their processes on the fly and introduce novel solutions to challenges.
"Technology helps us transform our manufacturing process, making it more sustainable and resilient," notes Tom Reitz, a renowned industry analyst.Virtual reality and augmented reality are also stepping into the limelight, offering immersive training sessions for staff and simulating production scenarios that save time and resources. These technological strides are nudged forward by government schemes that encourage industry leaders to adopt and adapt, keeping them a step ahead in global competition.
In terms of data management, predictive analytics and machine learning are transforming data into actionable insights. Manufacturers can now strategize with foresight, adjusting their supply chains proactively rather than reactively. This transition from traditional to technology-driven operations is supported by cybersecurity frameworks that guard valuable information against potential threats. There's a clear understanding that the future belongs to those who can efficiently harness the power of technology while ensuring data integrity and security. By integrating cutting-edge technological solutions, manufacturers not just meet the market demands, but they also stand as pioneers in sustainability efforts, reducing their carbon footprint, and promoting eco-friendly practices across their operations. Embracing technology is no longer optional; it is a prerequisite for survival and growth in the industrial landscape of today and tomorrow.
Government Schemes Supporting Manufacturing
Manufacturing has always been at the core of national economic growth and development, and recognizing this, various governments worldwide have rolled out schemes aimed at bolstering the manufacturing sector. In recent years, the focus has shifted not only to increasing output but also to embedding sustainability and competitiveness into the very fabric of this industry. These schemes aim to address the challenges of the ever-changing production landscape, geared towards enhancing the performance of the underlying manufacturing system components: people, processes, and technology.
One of the pivotal aspects these schemes target is upgrading technological infrastructure across manufacturing units. This often involves providing subsidies for installing new machinery or implementing innovative techniques that harness advances in AI and IoT. By integrating cutting-edge technology, manufacturers can not only boost efficiency but also maintain quality at every production stage. Ensuring that small and medium enterprises are not left behind, several initiatives offer financial aid specifically to these players, allowing them to compete on an equal footing with larger corporations.
Empowering the Workforce
Another critical area of government focus is the workforce, which forms the backbone of any thriving manufacturing enterprise. Training programs are put in place with the aim to upskill and reskill workers, making them adept at handling modern machinery and technology. Such schemes often include partnerships with academia to create a seamless transfer of knowledge and skills.
"Empowering workers is not just about enhancing skills; it's about reshaping mindsets," remarked a leading industry expert, illustrating the paradigm shift towards a more progressive and inclusive workforce.By focusing on human resources, these initiatives ensure that as technology evolves, the workforce is prepared and able to adapt accordingly.
Simplifying Processes and Reducing Costs
The streamlining of manufacturing processes is also central to these government initiatives. By providing guidelines and incentives for adopting lean manufacturing techniques, these schemes help minimize resource wastage and enhance production efficiency. Many programs encourage manufacturers to implement quality management systems that ensure continuous improvement. Incentives may include tax deductions or grants for companies that successfully reduce emissions as part of their lean transformations, aligning economic goals with environmental accountability.
Incentivizing Sustainable Practices
Addressing sustainability has become a primary objective, with schemes incentivizing practices that reduce carbon footprints and utilize renewable resources. Grants and subsidies for green technology installations such as solar panels, waste management systems, and water recycling facilities are commonplace. These incentives are designed to offset initial investment costs, making green choices more attractive to manufacturers. The potential for long-term savings and an enhanced public image only add to the allure of embracing ecological responsibility in the manufacturing sector. As more manufacturers embark on sustainable journeys, the collective impact is significant, contributing to global efforts against climate change.
Scheme | Description | Impact |
---|---|---|
AI Integration Grant | Offers subsidies for adopting AI technology | Increases efficiency by 20% |
Green Tech Subsidy | Funds for installing renewable energy systems | Reduces energy costs by 15% |
In essence, government schemes supporting manufacturing provide a multifaceted approach to fostering innovation and sustainability. By leveraging these initiatives, manufacturers not only enhance their production processes but also secure their position in an increasingly competitive market landscape. As these programs continue to evolve, the focus remains on creating a robust and resilient manufacturing ecosystem ready to face the challenges of tomorrow.
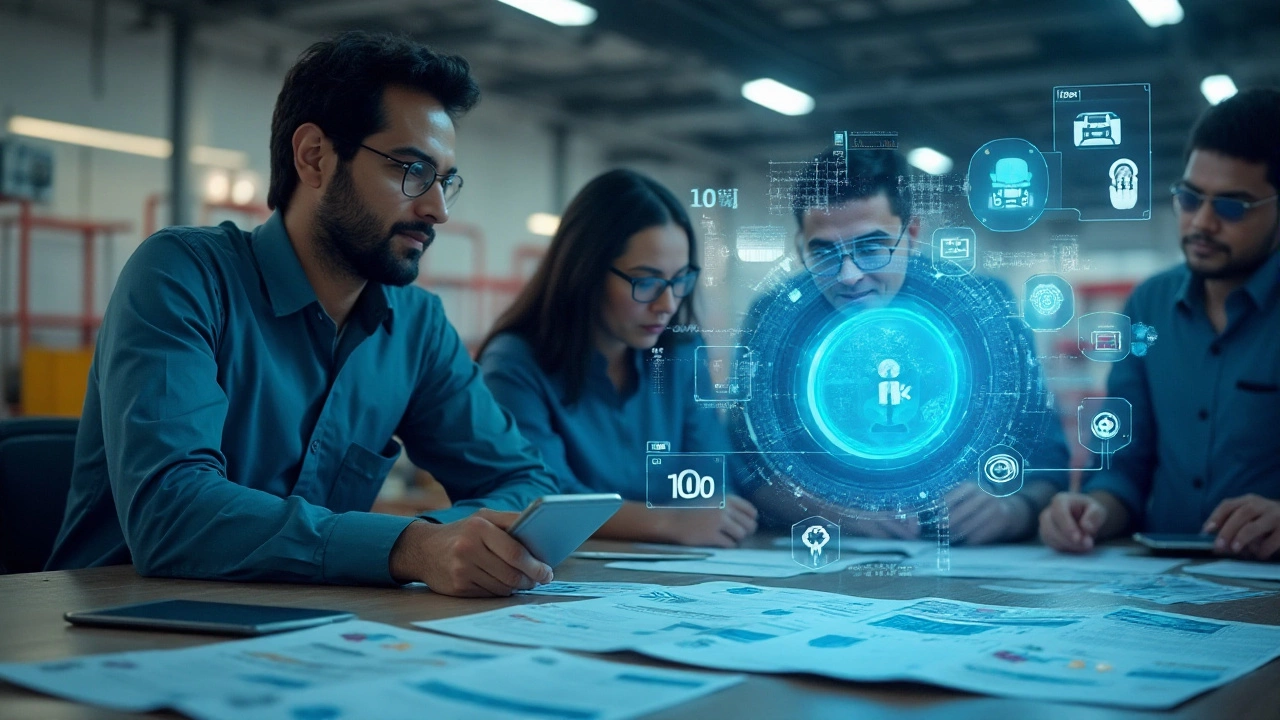
Future Trends in Manufacturing Systems
The transformation of manufacturing systems is poised for some fascinating developments. At the forefront, the integration of artificial intelligence and machine learning algorithms is revolutionizing both the planning and operational procedures across industries. These technologies enable machines to not just perform tasks, but to also predict maintenance needs, optimize scheduling, and even refine their own performance without human intervention. This leap in predictive maintenance can significantly reduce downtime, thereby enhancing efficiency and cutting costs, a critical concern for every manufacturing system.
The shift towards sustainable and green manufacturing is another forward-looking trend that cannot be overstated. More manufacturers are beginning to adopt eco-friendly practices, from recycling waste materials to using renewable energy sources. By 2025, you can witness an increased emphasis on the circular economy, where resources are reused and recycled, minimizing waste production. This trend doesn't only fulfill environmental responsibilities but also aligns with new, eco-conscious consumer expectations. As reported by a Deloitte study, ‘companies that invest in sustainable practices see not only increased operational efficiency but greater consumer trust as well.’
The advent of the Internet of Things (IoT) is changing how manufacturers approach logistics and supply chain management. Real-time data from smart devices allows for instantaneous adjustments to the supply chain, creating an agile, responsive production process that caters optimally to fluctuating market demands. Such agility is invaluable, especially with the unpredictability that recent global disruptions have underscored. With IoT-enabled systems, manufacturers can reduce lead times and manage inventories more effectively, which in turn escalates customer satisfaction.
Government schemes are also propelling the industry into the future by providing incentives and subsidies to companies that invest in research and development of innovative manufacturing solutions. Various programs are aimed at encouraging the adoption of emerging technologies like 3D printing, which allows for rapid prototyping and more personalized product designs. These governmental initiatives aim to boost domestic production capabilities and enhance global competitiveness.
The manufacturing industry is undoubtedly on the cusp of a digital transformation, with automation and big data analytics set to redefine traditional manufacturing processes. The data collected enables more profound insights and data-driven decision-making. Trends suggest an increasing reliance on cloud computing for secure, scalable, and efficient data management. As noted by the World Economic Forum, the companies leading this digital shift are likely to set new benchmarks for the industry standards.
In conclusion, the future of manufacturing systems is both promising and challenging. While technology continues to push the boundaries of what's achievable, the human element remains crucial, driving innovation, ensuring ethical practices, and managing transitions seamlessly. The path forward is an exciting one, blending technology, sustainability, and human ingenuity for the next chapter of industrial evolution.
Write a comment