You’ve probably heard people say, “America doesn’t make anything anymore.” When it comes to steel, that’s not exactly true—but the story has a few twists. The US still produces a hefty amount of steel, just not the way your grandpa might remember. Giant smoke-belching mills along the rivers? Some are still hanging on, but new players and new tech have changed almost everything.
If you're in construction, manufacturing, or just curious where your truck’s frame comes from, knowing how and where US steel gets made actually matters. Whether you care about jobs, quality, national security, or shorter supply chains, the steel story is all about the little details. Next time you see 'Made in America' stamped on a tool or appliance, there's a whole industrial journey behind that label. Let's get into what US steel manufacturing looks like right now, who’s doing it, and why it matters more than you think.
- What's Left of American Steel Plants?
- How US Steel Gets Made Today
- Challenges and Why It Matters
- Tips and Trends: Buying US-Made Steel
What's Left of American Steel Plants?
If you think the US steel industry is just history, think again. America still makes a ton of steel. In 2024, the US cranked out roughly 80 million metric tons of steel, making it the world’s fourth-largest steel producer after China, India, and Japan. That’s miles away from the 1970s peak, but it’s no small potatoes.
But don’t picture rows of creaky old smokestacks. Most US steel today comes from newer facilities called "mini-mills." These places mostly use scrap metal and electric arc furnaces—way more efficient than the old blast furnaces. Big names still in the game? Yeah, you’ll see companies like Nucor, Cleveland-Cliffs, and U.S. Steel running plants across states like Indiana, Texas, and Alabama.
The old massive integrated mills—giants you’d see in movies—haven’t totally vanished, but they’ve shrunk a lot. Some are still working in places like Gary, Indiana and Burns Harbor, but most new investment is going into high-tech, flexible operations. Here’s what the lay of the land looks like for US steel right now:
- Nucor runs over 20 mini-mills spread around the country and is the largest US steel producer today.
- Cleveland-Cliffs, mainly known for iron ore, now has major steelmaking sites in Ohio, Indiana, and Michigan.
- U.S. Steel still owns classics like the Gary Works in Indiana and Big River Steel in Arkansas.
Check out these recent stats for a snapshot of modern American steel:
Company | Main Plant Locations | 2024 Output (Million Metric Tons) |
---|---|---|
Nucor | S. Carolina, Texas, Alabama, Missouri, Arizona + more | approx. 22 |
Cleveland-Cliffs | Indiana, Ohio, Michigan | approx. 16 |
U.S. Steel | Indiana, Arkansas, Pennsylvania | approx. 9 |
So, there’s fewer plants than in the glory days, but the ones left are quick, high-tech, and mostly automated. North America’s steel scene is leaner, but it’s not dead—and it’s a lot smarter than before.
How US Steel Gets Made Today
When people think about steel mills, a lot of them imagine old-school blast furnaces. But here’s the twist: today’s US steel industry runs mostly on electric arc furnaces (EAFs). These are way more efficient and use scrap metal as the main ingredient. So, instead of digging up tons of iron ore and coal, most new American steel gets its start as recycled cars, appliances, and construction leftovers.
Now, blast furnaces aren’t totally gone. Some older plants, like U.S. Steel’s Gary Works in Indiana or Cleveland-Cliffs' Indiana Harbor, still use traditional methods, mostly to churn out steel for auto and infrastructure work. But the real growth is in EAF plants, which are popping up in states like Alabama, Arkansas, and Texas. Modern companies like Nucor and Steel Dynamics rely almost entirely on these high-tech scrap melters.
What makes EAFs a big deal? Check out this quick breakdown:
- Electric arc furnaces use about two-thirds the energy of blast furnaces.
- Roughly 70% of US steel production now comes from EAFs.
- EAF plants fire up much faster, shut down easily, and can switch what they make depending on market demand.
- Most EAF steel is made from at least 90% recycled material.
Here’s what the last few years looked like for US steel output, to give you the real picture:
Year | Total US Raw Steel Production (million tons) | % Produced by EAFs |
---|---|---|
2021 | 86.0 | 72% |
2022 | 80.7 | 71% |
2023 | 81.1 | ~72% |
The US is still a steel heavyweight globally, usually top five in annual output. If you’re buying American steel now, odds are good it was cooked up in an EAF, not the iron-and-coal monsters from 50 years ago.
If you ever tour a modern mill (and a few let you), you’ll see fresh-faced operators tracking everything on computers—no more terrifying rivers of molten metal and soot-covered workers. It’s safer, greener, and surprisingly cool to watch. US steel makers are also pushing to use more renewable electricity and reduce emissions, which is why the plants of today look nothing like the ones from a generation ago.
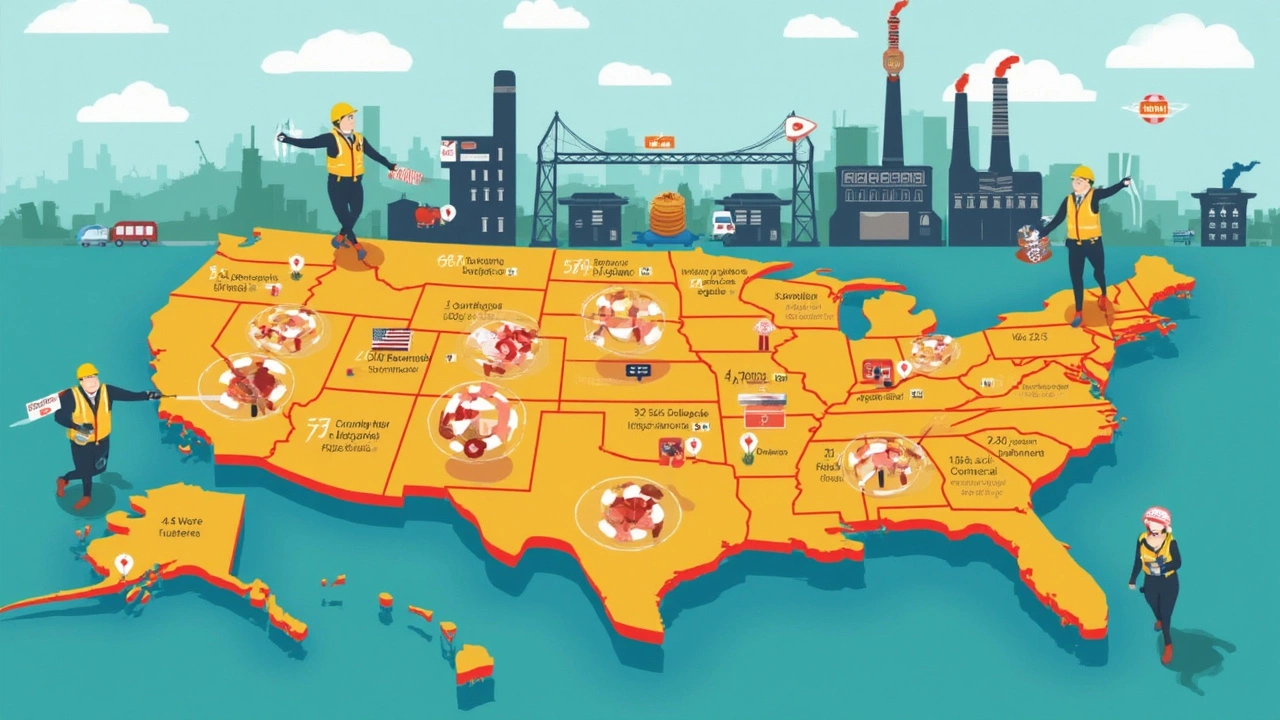
Challenges and Why It Matters
No way around it—making steel in the US is tough. Only about 4% of global steel is made here, and that’s a far cry from the heyday when steel towns ruled. The main headache is price. US labor is more expensive than overseas, and environmental rules are stricter. While that’s a bragging point for quality and safety, it does mean higher costs. Countries like China flood the world with cheaper steel, which pushes US plants to the edge.
Then there’s the tech side. Many American mills don’t use the old blast furnaces much anymore. Instead, they run electric arc furnaces (EAFs) that mostly melt scrap—faster and cleaner, but a different business entirely. That’s great for recycling, but it means the US imports a lot of what’s called 'virgin steel' for things that need special strength, like new cars or bridges.
Here’s why this matters to everyone, not just steelworkers:
- US steel means American jobs—not just in the mills, but trucking, mining, and engineering. When local plants shrink or close, whole communities feel it.
- National security depends on a steady local supply. During the early days of COVID-19 and global tensions with Russia, steel prices jumped, and folks suddenly realized how many industries depend on the stuff—from construction to defense.
- Quality is a real issue. US-made steel usually passes stricter inspections, so builders and manufacturers know what they’re getting. Cheaper imported steel can come with hidden risks.
- Buying American steel can help cut the carbon footprint compared to shipping tons of foreign steel across oceans, but it’s a trade-off—cost versus sustainability.
Consumers and businesses don’t always notice steel’s origins until there’s trouble. Price tags, reliability, and jobs all trace back to where and how that metal’s made. That’s why the conversation keeps coming up every election cycle and in every big building project.
Tips and Trends: Buying US-Made Steel
Trying to figure out if you're actually getting American steel and not just something labeled “imported”? Here’s what you’ll want to know if you’re shopping for steel—from small DIY projects to big commercial build-outs.
First off, the US steel industry puts a big focus on transparency and traceability. Look for a Mill Test Report (MTR)—it’s like a birth certificate for steel, telling you exactly where and when it was made. This paperwork is standard with real American-made products. If a supplier can’t show you, there’s a reason to be suspicious.
Don’t be fooled by “Buy America” and “Made in USA” claims on packaging. For government projects, steel needs to be melted and poured in the US to count. Many imported products get final touches here and slap on a flag, but they’re not the real deal. For bigger jobs, demand those origin documents.
- If you’re buying in bulk or for a business, use reliable distributors who specialize in certified domestic product. Companies like Nucor, Steel Dynamics, and U.S. Steel are major, US-based producers—ask your supplier if their stuff comes straight from them.
- For DIYers or small businesses, ask for “domestic” or “DFARS-compliant” steel at local yards—these terms often mean American-made, especially for structural and rebar products.
- Watch for price spikes and supply swings. In early 2024, domestic steel prices hit $1,100 per ton (up from an average $800 in late 2023), mainly from tight supply and high demand.
- Sheet steel, pipe, and rebar are the most commonly American-made steel products available on the open market. Specialty alloys or stainless? Those still often come from overseas, so double check.
The biggest trend? Clean steel. US mills are investing in electric arc furnaces (EAFs), which reuse scrap and cut carbon emissions. Nucor, for example, now has more EAFs than legacy blast furnaces, making them greener and more flexible when demand shifts.
Here’s a quick look at who’s leading the charge in the domestic market:
Company | 2024 US Production (million tons) | Main Product Types | Notable Trend |
---|---|---|---|
Nucor | 23 | Sheet, bar, structural | All EAF steel, large scrap operations |
U.S. Steel | 13 | Flat-rolled, tubular | Mix of old and new plants |
Steel Dynamics | 12 | Sheet, long products | New greenfield plants in Texas |
Last tip—keep an eye on government infrastructure spending. Big bills often come with strict buy-American clauses, which ramps up demand and can raise prices for everyone else. Planning ahead and working with local suppliers can save you a lot of headaches when the big projects start sucking up supply.
Write a comment